What Is Sheet Metal Stamping? How Does It Work?
- Clyde Verse
- 2024年3月27日
- 讀畢需時 12 分鐘
Brief Overview Of Sheet Metal Stamping
Sheet metal stamping is a versatile and efficient manufacturing process employed by companies like Neway to create precise and complex metal components. This method uses dies and punches to shape flat metal sheets into desired forms.
Sheet metal stamping typically begins with a flat metal sheet, often made of steel, aluminum, or other alloys. This sheet is placed between a die (female) and a punch (male). The punch exerts force on the sheet, causing it to deform and take the shape of the die. Depending on the part's complexity, the process can involve a single operation or a series of operations.
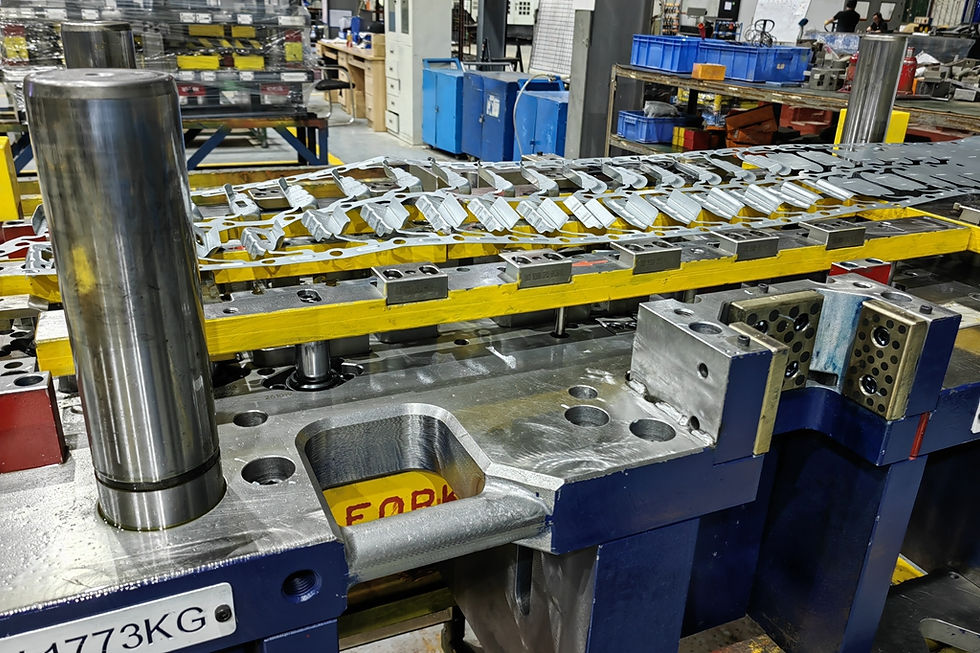
Key Features Of Metal Stamping
Precision: Stamping offers high precision, allowing for the production of intricate and detailed components with tight tolerances.
Speed and Efficiency: The rapid process makes it suitable for large-scale production. Neway optimizes production efficiency through advanced machinery and techniques.
Material Utilization: Stamping minimizes material waste as it maximizes the use of the metal sheet, contributing to cost-effectiveness.
Versatility: Sheet metal stamping can be adapted for various metals, sheet metal thicknesses, and complexities, providing flexibility in manufacturing.
Cost-Effective Production: Neway's expertise in stamping translates to cost savings through efficient material utilization and rapid production cycles.
Consistency: Stamping ensures consistent part quality, which is crucial for industries where precision is paramount.
Complex Geometry: The process allows the creation of components with intricate shapes and details, expanding design possibilities.
Mass Production Capability: Neway's stamping capabilities are well-suited for high-volume production, meeting the demands of diverse industries.
Importance Of Sheet Metal In Manufacturing
Sheet metal plays a pivotal role in the manufacturing landscape, and Neway, as a leading custom parts manufacturer, leverages sheet metal fabrication to meet diverse industry needs.
Versatility and Adaptability:
The adaptability of sheet metal makes it suitable for various applications across industries. Such as consumer electronics battery conductive shrapnel, telecommunication shell, housing, boxing, and lighting solution brackets
Neway excels in utilizing sheet metal's versatility, offering tailored solutions for clients with varying requirements.
Precision Manufacturing:
Sheet metal fabrication, including cutting, bending, and stamping, allows for high precision in creating intricate components. Usually, the thickness of stamping is most suitable between 0.2mm and 3.0mm, and Neway can guarantee accuracy within +/-0.4mm. The highest can reach +/-0.1mm.
Neway's commitment to precision ensures the delivery of accurate and consistent sheet metal parts.
Cost-Effectiveness:
Efficient material usage in sheet metal fabrication contributes to cost-effectiveness. It has an irreplaceable position, especially for producing customized sheet parts.
Neway's expertise lies in optimizing production processes, translating into cost savings for clients.
Speed and Efficiency:
Rapid prototyping and production cycles are achievable through sheet metal fabrication. The design and manufacturing of stamping molds have shorter development cycles than molds such as casting and injection molding, which means lower cost.
Neway's emphasis on efficiency ensures timely delivery of custom parts without compromising quality.
Customization Possibilities:
Sheet metal's malleability enables the creation of custom parts with diverse shapes and sizes. Neway provides custom parts stamping processing in four processes: Progressive Die Stamping, Deep Drawn Metal Stamping, Transfer Die Stamping, and Multi-Slide Metal Stamping.
Neway's one-stop service includes sheet metal fabrication, offering clients tailored solutions for their unique specifications. It can provide almost all sheet metal parts processing.
Structural Integrity:
Sheet metal components often exhibit high structural integrity, which is crucial for applications where strength and durability are paramount, such as stamped 3D printer internal brackets, car seat belt buckles, and luggage accessories, which have durability and aesthetics.
Neway's quality control measures ensure that fabricated sheet metal parts meet rigorous standards for structural performance.
Integration with Other Processes:
Sheet metal fabrication integrates with other manufacturing methods, such as welding and riveting. For example, adding riveting process, laser welding process based on stamping,
Neway's holistic approach to manufacturing allows for the seamless incorporation of sheet metal components into larger assemblies.
Neway's Expertise In Sheet Metal Fabrication
Sheet metal fabrication is a versatile manufacturing process that involves shaping metal sheets through various techniques, such as laser cutting, stamping, and bending. Neway, a leading custom parts manufacturer, excels in sheet metal fabrication, providing a comprehensive range of services to meet diverse industry needs.
One of the critical processes in sheet metal fabrication, laser cutting, utilizes a focused laser beam to cut through metal sheets precisely. Neway employs state-of-the-art laser cutting technology, ensuring accuracy and efficiency in creating intricate designs and shapes.
Metal stamping is a cost-effective method Neway uses to produce large quantities of identical metal components. The process involves a stamping press that molds the metal into the desired shape using dies and punches. It allows for the rapid production of parts with high precision and consistency.
In sheet metal fabrication, metal bending is crucial in shaping metal sheets into specific forms. Neway utilizes advanced metal bending equipment, ensuring precise bends and angles are created according to customer specifications.
Advantages of Stamping Processing:
Stamping processing, as employed by Neway, offers several advantages. It is a highly efficient method for mass production, ensuring cost-effectiveness. The process enables the creation of complex and detailed parts with tight tolerances, showcasing Neway's commitment to delivering high-quality custom parts.
Neway's Expertise:
A commitment to excellence and cutting-edge technology distinguishes Neway's expertise in sheet metal fabrication. By leveraging their proficiency in laser cutting, metal stamping, and metal bending, Neway provides a one-stop solution for clients seeking custom sheet metal components.
In conclusion, Neway's sheet metal fabrication services encompass a comprehensive array of techniques executed precisely and efficiently. This expertise makes Neway a reliable partner for industries requiring top-tier custom metal components.
Basics of Sheet Metal Stamping
Definition And Purpose Of Sheet Metal Stamping
Sheet metal stamping is a versatile manufacturing process employed by Neway to shape and form metal sheets into desired components. This method involves using a stamping press to exert force on a metal sheet, transforming it into a specific shape or configuration. Neway utilizes various techniques within sheet metal stamping, including Progressive Die Stamping, Deep Drawn Metal Stamping, Transfer Die Stamping, and Multi-Slide Metal Stamping, to cater to diverse client needs.
The purpose of sheet metal stamping is to mass-produce precise and intricate metal parts efficiently and cost-effectively. By employing techniques like laser cutting, Neway ensures the accurate and rapid shaping of metal sheets. Metal stamping, another vital aspect, involves using dies and punches to create consistent, high-quality parts.
One of the critical advantages of sheet metal stamping is its ability to produce components with tight tolerances, ensuring uniformity and precision. This process also allows for the creation of complex geometries, contributing to the versatility of Neway's manufacturing capabilities. Furthermore, sheet metal stamping is a rapid and efficient method, facilitating high-volume production to meet the demands of various industries.
Overview of Materials Used in Sheet Metal Stamping
In sheet metal stamping, the selection of materials plays a crucial role in ensuring the quality and functionality of the final products. Neway, a leading custom parts manufacturer, employs various materials in sheet metal fabrication processes, including laser cutting, stamping, and bending. Let's overview the materials commonly used in sheet metal stamping.
Steel Alloys:
Overview: Steel alloys are widely used in sheet metal stamping for their excellent strength, durability, and formability.
Neway's Advantage: Neway specializes in precision stamping of steel alloys, offering clients a diverse range of options such as carbon steel, stainless steel, and high-strength alloys.
Aluminum Alloys:
Overview: Aluminum alloys are favored for their lightweight properties, corrosion resistance, and conductivity, such as Aluminum 6061, 6063, 7075, Etc.
Neway's Advantage: Neway's expertise in stamping aluminum alloys facilitates the production of intricate and lightweight components, meeting the demands of diverse industries.
Copper and Brass Alloys:
Overview: These alloys are valued for their conductivity, corrosion resistance, and aesthetic appeal and are often used in parts with conductive properties, such as conductive springs, battery electrodes, etc.
Neway's Advantage: Neway's precise metal stamping processes extend to copper and brass alloys, ensuring the creation of components with functional and visual appeal.
High-Strength Alloys:
Overview: High-strength alloys are essential for applications demanding enhanced mechanical properties.
Neway's Advantage: Neway's proficiency in working with high-strength alloys positions them as a reliable partner for industries requiring robust and resilient sheet metal components.
Exotic Metals:
Overview: Exotic metals, such as titanium or nickel alloys, find applications in specialized industries with stringent requirements.
Neway's Advantage: Leveraging its advanced manufacturing capabilities, Neway can handle exotic metals precisely, meeting clients' unique needs in cutting-edge sectors.
Neway's commitment to quality and diverse material expertise in sheet metal stamping ensures clients receive tailored solutions that align with the highest industry standards. This comprehensive approach and Neway's dedication to client satisfaction distinguishes them as a reliable and innovative force in the custom parts manufacturing landscape.
Tolerance Of Sheet Metal Stamping
In sheet metal stamping, the selection of materials plays a crucial role in ensuring the quality and functionality of the final products. Neway, a leading custom parts manufacturer, employs various materials in sheet metal fabrication processes, including laser cutting, stamping, and bending. Let's overview the materials commonly used in sheet metal stamping.
Steel Alloys:
Overview: Steel alloys are widely used in sheet metal stamping for their excellent strength, durability, and formability.
Neway's Advantage: Neway specializes in precision stamping of steel alloys, offering clients a diverse range of options such as carbon steel, stainless steel, and high-strength alloys.
Aluminum Alloys:
Overview: Aluminum alloys are favored for their lightweight properties, corrosion resistance, and conductivity, such as Aluminum 6061, 6063, 7075, Etc.
Neway's Advantage: Neway's expertise in stamping aluminum alloys facilitates the production of intricate and lightweight components, meeting the demands of diverse industries.
Copper and Brass Alloys:
Overview: These alloys are valued for their conductivity, corrosion resistance, and aesthetic appeal and are often used in parts with conductive properties, such as conductive springs, battery electrodes, etc.
Neway's Advantage: Neway's precise metal stamping processes extend to copper and brass alloys, ensuring the creation of components with functional and visual appeal.
High-Strength Alloys:
Overview: High-strength alloys are essential for applications demanding enhanced mechanical properties.
Neway's Advantage: Neway's proficiency in working with high-strength alloys positions them as a reliable partner for industries requiring robust and resilient sheet metal components.
Exotic Metals:
Overview: Exotic metals, such as titanium or nickel alloys, find applications in specialized industries with stringent requirements.
Neway's Advantage: Leveraging its advanced manufacturing capabilities, Neway can handle exotic metals precisely, meeting clients' unique needs in cutting-edge sectors.
Neway's commitment to quality and diverse material expertise in sheet metal stamping ensures clients receive tailored solutions that align with the highest industry standards. This comprehensive approach and Neway's dedication to client satisfaction distinguishes them as a reliable and innovative force in the custom parts manufacturing landscape.
Four Types of Shee Metal Stamping
Progressive die stamping, deep-drawn metal stamping, transfer die stamping, and multi-slide metal stamping are distinct metal stamping processes with unique characteristics and applications.
Progressive Die Stamping
Progressive die stamping is a highly efficient and versatile sheet metal fabrication method employed by manufacturers like Neway. In this process, a metal strip is fed through a series of stations within a single die, progressively forming the desired shape with each step. Let's delve into the description, advantages, and applications of progressive die stamping.
Description:
Progressive die stamping involves a continuous process where a metal strip moves through various stations in a die, each station performing a specific operation. These operations can include cutting, bending, punching, and coining. The final product is obtained as the metal strip progresses through the die, with each station contributing to the overall shape and features of the part.
Advantages:
Cost-Efficiency: Progressive die stamping is cost-effective for high-volume production, allowing rapid and continuous manufacturing.
Precision and Consistency: The process ensures high precision and consistency in part dimensions, reducing the likelihood of defects.
Speed of Production: Due to its continuous nature, progressive die stamping enables rapid production cycles, contributing to shorter lead times.
Material Utilization: Minimizes material wastage as the progressive die optimally uses the metal strip, making it an environmentally friendly option.
Complex Geometry: Proving intricate and complex parts with multiple features in a single operation.
Applications:
Automotive Industry: Progressive die stamping is widely used in the automotive sector for manufacturing components such as brackets, panels, and chassis parts.
Electronics: The method is employed for creating precise and small components used in electronic devices, ensuring uniformity and quality.
Appliances: Manufacturers use progressive die stamping to produce parts for household appliances like washing machine panels, refrigerator components, and more.
Hardware and Tools: Various hardware components and tools benefit from the efficiency of progressive die stamping, meeting the demand for high-volume production.
Consumer Goods: Items like metal casings, brackets, and other components in consumer goods often undergo progressive die stamping for mass production.
By incorporating progressive die stamping into its manufacturing techniques, Neway exemplifies its commitment to providing efficient, high-quality solutions for custom metal parts across diverse industries. The streamlined production process, cost-effectiveness, and precision make progressive die stamping valuable in Neway's one-stop service for custom parts.
Deep Drawn Metal Stamping
Deep-drawn metal stamping is a versatile manufacturing process to create cylindrical or box-like shapes from flat sheet metal. By applying force to the metal, it's formed into a desired shape using a series of dies and punches. Here's a breakdown of its description, advantages, and applications:
Description:
Deep-drawn metal stamping involves several steps:
Blanking: Cutting the metal sheet into a round or shaped blank.
Drawing: Placing the blank into a die and using a punch to form it into a cup-like shape.
Redrawing: Stretch and shape the cup further to achieve the desired depth.
Trimming: Cutting off excess material to finalize the shape.
Advantages:
Cost-Efficient: Suitable for high-volume production, reducing per-unit costs.
Complex Shapes: Capable of forming intricate and complex shapes with high precision.
Material Savings: Minimizes material waste by utilizing sheet metal efficiently.
Strength and Durability: Produces solid and durable parts due to the metal's inherent properties.
Consistency: Provides uniformity and consistency in part production.
Applications:
Automotive Industry: Used in manufacturing vehicle components like brackets, enclosures, and structural elements.
Household Appliances: Parts for kitchen appliances, HVAC systems, and various household items.
Aerospace: Creating components for aircraft structures and systems.
Medical Devices: Forming parts for medical equipment and devices.
Electronics: Producing casings, connectors, and components for electronic devices.
This method's ability to create precise, durable parts makes it valuable across multiple industries, providing cost-effective solutions for complex production.
Transfer Die Stamping
Transfer die stamping is a highly efficient and versatile sheet metal fabrication method in manufacturing. This process, which falls under the broader category of precision sheet metal fabrication, is notable for its speed, accuracy, and cost-effectiveness.
Description:
Transfer die stamping involves using a die set to shape and cut metal sheets into specific forms. The term "transfer" in transfer die stamping refers to the movement of the metal workpiece from one station to another within the die set. The die set consists of multiple stations, each performing a distinct operation on the material.
Advantages:
High Production Speed: One of the critical advantages of transfer die stamping is its rapid production capabilities. The automated and sequential nature of the process allows for a high volume of parts to be produced in a relatively short period.
Precision and Consistency: Precision dies ensure accurate shaping and cutting of the metal sheets, leading to consistent and high-quality parts. It is crucial in industries where tight tolerances and uniformity are paramount.
Cost-Effectiveness: Transfer die stamping is a cost-effective method for large-scale production. The efficiency of the process, coupled with reduced labor requirements due to automation, contributes to lower per-unit manufacturing costs.
Versatility: This method suits various materials, including metals and alloys. It accommodates different sheet thicknesses, making it versatile for diverse applications.
Applications:
Automotive Industry: Transfer die stamping is extensively used in the automotive sector for manufacturing components such as body panels, chassis parts, and structural elements. The high-speed production aligns well with the demands of the automotive assembly line.
Consumer Electronics: The precision and consistency offered by transfer die stamping make it suitable for producing intricate components used in consumer electronics, such as casings, connectors, and brackets.
Appliance Manufacturing: Household appliances often require stamped metal parts for structural integrity and aesthetic appeal. Transfer die stamping is commonly employed to produce components for appliances like washing machines, refrigerators, and ovens.
Industrial Equipment: Various industrial equipment and machinery rely on transfer die-stamped parts for their structural components, ensuring durability and reliability in demanding environments.
In conclusion, transfer die stamping is highly efficient and cost-effective with applications across industries. Its ability to deliver precision, speed, and versatility makes it a valuable process in sheet metal fabrication. As Neway excels in sheet metal fabrication, integrating transfer die stamping into production processes aligns with the company's commitment to delivering high-quality custom parts efficiently.
Multi-Slide Metal Stamping
Multi-slide metal stamping is a highly efficient and versatile metal forming process employed by manufacturers like Neway to produce intricate metal parts. This precision technique involves using multiple slides or tooling mechanisms that enable complex shapes to be stamped with remarkable accuracy. Let's delve into the description, advantages, and applications of this innovative manufacturing method.
Description:
Multi-slide metal stamping, a subset of metal stamping, utilizes advanced machinery with multiple slides working in tandem. Each slide carries out a specific forming operation, contributing to creating intricate components. The synchronized movement of these slides allows for the production of complex geometries with tight tolerances. This method is particularly effective for high-volume production, making it an ideal choice for Neway's one-stop custom parts service.
Advantages:
Precision and Complexity: Multi-slide stamping creates high-quality intricate parts, ensuring consistency across large production runs.
Material Utilization: The process minimizes material waste, contributing to cost-efficiency and aligning with sustainable manufacturing practices.
High-Speed Production: With multiple slides working simultaneously, the cycle time for each part is significantly reduced, leading to faster production rates than traditional stamping methods.
Versatility: Multi-slide stamping is adaptable to various materials, including metals, which aligns with Neway's diverse manufacturing capabilities.
Applications:
Electronics Industry: Multi-slide stamping is widely used in producing intricate connectors, terminals, and other small, precise components critical to electronic devices.
Automotive Sector: Neway can leverage this technique for manufacturing small, intricate automotive parts such as brackets, clips, and connectors, meeting the industry's demand for precision and efficiency.
Medical Devices: The medical field benefits from multi-slide stamping for producing tiny, complex components used in medical devices, ensuring reliability and accuracy.
In summary, multi-slide metal stamping is a cutting-edge manufacturing process that aligns seamlessly with Neway's one-stop service for custom parts. Its precision, efficiency, and versatility make it a valuable tool for industries requiring intricate components, allowing Neway to consistently deliver high-quality solutions to its clients.
Comments